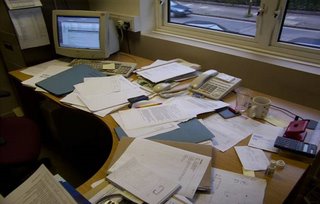
Create the office systems your business deserves!!!
By John Hicks M.IDM
Managing Director of Headline Promotions, Press & PR
UK manufacturing may be on the ropes but it is not down and out!
They certainly lead the way in developing new techniques and technology, and adapting Japanese methodology, to make their businesses efficient and effective.
For many years, though, improvement activities have been a focus for manufacturing and engineering businesses. However, most of this focus has been around the improvements available on the factory floor and how the product is actually put together.
Although these improvement initiatives have offered significant improvements to organisations, there is an unfortunate fact that, behind the scenes, lies a mass of non-value adding activity.
Walk into most offices from all areas of the business world and you will see desks piled high with paper, people moving around and a heightened level of activity. Whether or not these areas of the organisation are meeting their objectives is hard to gauge and, unfortunately, we tend to find out when it is too late.
With customers demanding more from organisations, the pressure on to find more and more time and cost savings within the business.
It is in the area of the office where some interesting work is being undertaken in the UK, led by the manufacturers’ membership organisation, the Engineering Employers’ Federation’s southern regional team (EEF South) (http://www.eefsouth.org).
Working in association with SEEDA, the South East’s regional development agency, and the European Social Fund, EEF South are running a programme entitled Lean Office. Senior consultant David Fletcher leads the project.
“The objective of the programme is to share our expertise with organisations and to provide hands on training staff in the office and support functions of businesses. This will help them create processes that integrate into their business to ensure a smooth flow of information and product from sale or enquiry through to delivery to customer both internally and externally.” says Fletcher.
“Typical tangible lean improvements have been a lead time reduction of up to 50%, reduction of order entry time of up to 50%, reduced finished goods and raw material stock levels reduced expediting time, reduced rework levels increased available operational time, improved communication and improved customer satisfaction” he added.
So these are the typical tangible improvements but what about some intangibles? Fletcher suggests that implementation of the lean office usually leads to stronger linkages between departments, improved internal communication between departments, empowering employees to drive improvements and releasing talent within employees.
On their website, EEF South cites a number of interesting case studies. For example, Metaltech Precision Engineers Ltd, based in East Sussex, is a sub-contracting company, acknowledged as a strategic supplier of precision machined components and sub assemblies for a variety of customers with a variety of needs.
With a multitude of customers and prospective customers each sending a myriad of component and sub-assembly enquiries to Metaltech each year, the company has had to manage a very complex front-office document storage and retrieval system.
Recognising that they could improve their competitive advantage by shortening the lead-time from enquiry through to delivery, the directors at Metaltech viewed the ESF funded Lean Office Programme, delivered by EEF South by consultant Tim Franklin, as an excellent programme to facilitate such a strategic improvement.
As well as benefiting the customer with a quicker turnaround time, the management team could also redirect time saved to other strategic business improvements.
Ken Elphick, Managing Director, Metaltech Precision Engineers Ltd. reports that “the lean office programme equipped Metaltech staff with an understanding of just what office-based improvements are possible, and has provided a platform that allows us to conduct regular continuous improvement activities”.
Smaller businesses get free or subsidised in-depth advice and training from some of the UK’s leading business improvement consultants so have little or nothing to lose!
So, where next? Fletcher says “There is still much to do in the manufacturing sector here in the UK to bring them the benefits of the lean office approach. However, the tools and techniques apply to any office or support function in any organisation but retail and the professions such as lawyers or estate agents.”
This article was published by The American Chronicle series in May 2006.
Copyright Headline Promotions, Press & PR